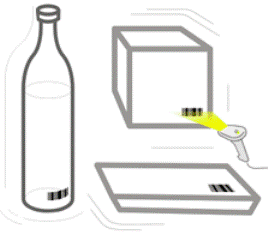
ICHNOS is a traceability integrated system developed by ENTEF company, which covers the needs through one and only application. By observing the products and the production lines of a company, it provides assurance and sequrity for both the consumer and the producer. It offers the ability for thorough tracing throughout the entire production line, aiming for their quality reservation and the efficiency in searching and projecting every single batch from its production line (producer) to the consumer.
The easy and fast recall of defective batches is ensured in cases of inevitable errors that frequently occur in the production line. The type and variety of the information keeped in a traceability system differs and varies according to each company's goals and needs and depend on more factors like:
- The product's nature
- The farming and/or industrial practices
- The customer's specifications
- The legislation and standard demands
The ENTEF' ICHNOS practical goal is recording, tracing and presenting the information related to the production of each and every product. This information is being presented after search, using as search criteria the package's label LOTNUMBER of the final product or the code of the materials used for the production. Thus, the presentation of all phases can be made from the collection of the materials and raw materials used, to the delivery of the final product and reversely.
The ICHNOS system comprises of a main server, where the system's central management application is installed. In cases where other automatation systems are used during the production process, a specially designed protocol is being used in order for the communication to be achieved.
The central management application communicates with a Data base, where all the information is being stored. What is more, the system comes with all the essential devices for generating barcode labels and reading barcodes. These barcode labels that are being placed on the product's package facilitate on the utmost extent the search and presentation of the entire information behind the product's code.
Generally, the production process splits up to the following phases:
Phase A: Raw material collection by the producer
Phase B: Raw material concentration and storage
Phase C: Raw material processing
Phase D: Final product and packaging generation
Phase E: Final product delivery to customer
In each of the above phases of the production process, the entire information that labels it is being recorded.
There are two patterns that can be followed for the collection of the information needed in order for the system's proper operation:
Manually: specially trained and accredited users enter the information through a computer (pc). The data entry forms are designed so that they are user friendly and easy to use, even if the user is not familiar with the use of computers.
In every data entry stage to the system, the management application guides the operator through relevant checks and notifications about his potential mistakes.
By using automated devices and systems: nearly avery machine and device that takes part in the production process, generates information that can be transfered to the system's log file via specially manifactured automated devices. This use of automation in the production minimizes the time needed for recording the data, while maximizes the system's credibility.